SmartOrdering: standing the test of time with flying colours
23.06.2024
As a market leader for fastening technology, Bossard supplies production sites worldwide with help from smart logistics systems. The innovative company has been using an AI system from Ergon since 2018. SmartOrdering automates and optimises the procurement process with machine learning. In this interview, Marion Keller, Global Director of Smart Factory Logistics at Bossard, explains how the system has stood the test of time.
The business of Bossard is the logistics of C-parts, which are small parts such as screws, nuts or seals. They are important for the assembly of systems and devices. Missing C-parts can result in blocked production lines and costly express deliveries. To avoid this, Bossard developed its ARIMS platform. With the help of SmartBins, the platform monitors stock levels in real time and places orders automatically when stock levels fall below a certain point. Bossard worked together with Ergon to create the SmartOrdering AI system with a view to simplifying the time-consuming process of managing order parameters. The system continuously monitors the consumption of C-parts and automatically defines ideal order parameters using machine learning. So, how exactly has the system helped Bossard since it was implemented in 2018? Marion Keller, Global Director of Smart Factory Logistics at Bossard, tells us everything.
Marion Keller, the pilot project for SmartOrdering at Bossard got underway in 2018. How exactly has it helped the company since then?
We started the pilot phase with 30 clients. Today, 66 per cent of our clients use SmartOrdering. Our goal is to increase this figure to 80 per cent. To achieve this, we continuously assess which of our clients’ needs are not covered yet. Some clients like to have plenty of stock in their warehouses at all times, while others want to store as few goods as possible. As a client-focused company, we have to cover a lot of different needs. The system helps us enormously in this area and has more than proven its worth over the past five years.
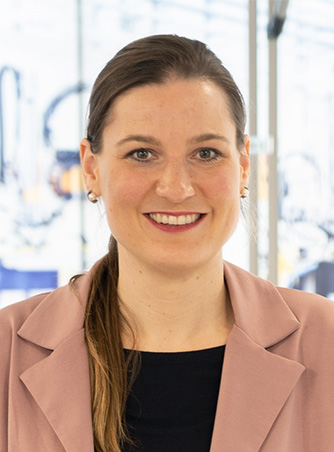
“The algorithm has been working autonomously for more than five years now. Regardless of whether a client consumes more or fewer C-parts, the algorithm continuously adjusts the order parameters and thus helps us to save money and conserve resources.”
What are the advantages of SmartOrdering?
SmartOrdering helps us to save internal resources and allows us to be much more flexible. Regardless of whether a client consumes more or fewer C-parts, the algorithm quickly responds to any changes and continuously adjusts the order parameters. This allows us to optimise transport and only ship goods when they are really needed. We also end up having to send out far fewer express orders, which saves a great deal in both money and resource terms. For lots of clients, SmartOrdering means having an optimised inventory, which is advantageous in terms of consumption, availability and inventory costs.
How autonomous is the algorithm?
The algorithm analyses how many products a client has consumed in the last 365 days, what exactly they have taken out of their warehouse, when the next delivery is and whether the remaining items will last until then. The system uses all of this information to calculate the ideal order quantities and best order times for the future. It does all of this autonomously. It only requires human interaction in exceptional cases, such as when a client sees that they will need significantly more parts in three weeks’ time, for example. The algorithm does not have this type of information.
Sustainability is important for Bossard. What role does SmartOrdering play in this respect?
I’ve actually already briefly touched on this. We save on both transportation journeys and work steps, and largely avoid express orders. We can also see the stock levels of our clients in the system and can incorporate this information into our supply chain. For our clients, optimised storage is a plus point for their sustainability practices.
What are the most important things that you have learned since implementing this system?
The biggest thing that we have learned is that we have to reassure our clients and help them to trust SmartOrdering, even if they do not fully understand the algorithm. It can be hard to understand that even the algorithm cannot stop certain stockouts, like when a year’s supply of a certain part is taken out at once, for example. We have to give our staff the tools so that they can explain to their clients that neither people nor the algorithm can predict certain events. That is why we are currently investing a great deal in training our teams.
Is the system used globally?
Yes. For us, this is important. When we do something, it needs to work for all countries. We always try to make things as standardised as possible, then we use parameters to adapt them to individual regions and countries. Different cost parameters for different countries have already been included in the algorithm. Interestingly, though, we have not had to adapt the standard parameters yet.
What future developments does Bossard have in its pipeline?
We are currently trying to find out what is stopping the other 34 per cent of our clients from using SmartOrdering. We are constantly launching initiatives in this respect to create greater transparency. For example, clients can see just how much the algorithm could help them save on their dashboard. We are also working on finding ways to better display more information about the algorithm. At the same time, we are looking into how and where adjustments need to be made to the system to attract more clients. Another question we are trying to answer is how we can give the algorithm all the information that it does not have yet. For example, if a client shares a forecast with us, the system should include this in its calculations in the future. We also want to enrich the algorithm with more data so that it has even more information. There is a lot to look forward to!