Optimising inventory levels with machine learning
01.04.2020 – Bossard reference
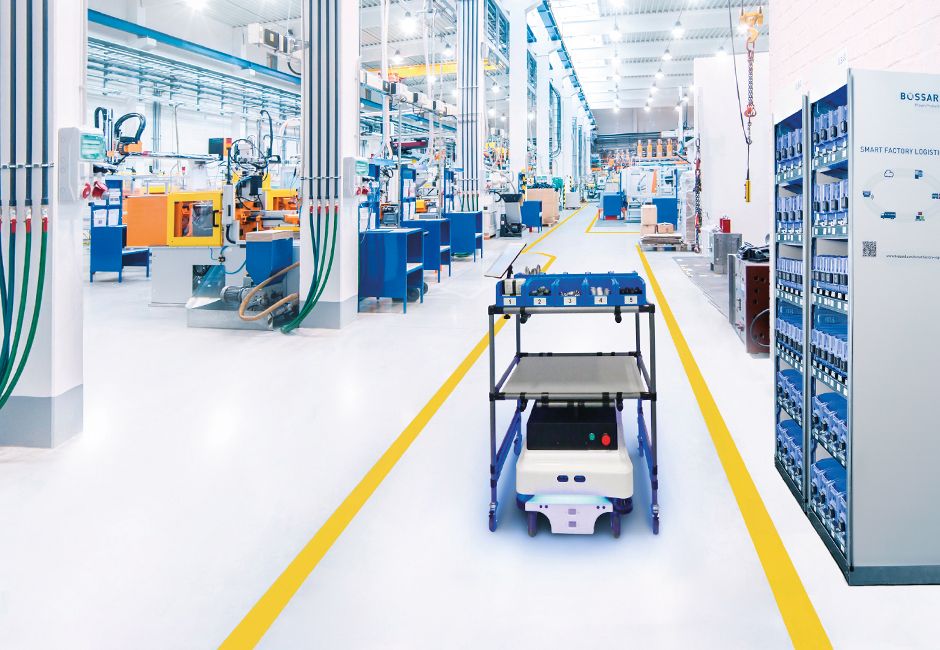
Bossard, a market leader in fastening technologies, uses intelligent logistics systems to supply production plants worldwide. The company’s success is underpinned by the highest standards of quality combined with ongoing product development. Its latest innovation in the field of smart factory logistics is SmartOrdering – a system that uses machine learning to automate and optimise the procurement process. The results include increased availability of C-parts for customers, 70 per cent fewer express deliveries and significant cost savings.
The Zug-based company has specialised in the logistics of C-parts (small components like screws, nuts and seals) that are key elements when assembling machinery and devices. Such parts are cheap to procure but can entail high costs when they are not available – production can grind to a halt, necessitating expensive express deliveries. Bossard has developed its ARIMS platform to prevent such an eventuality. Thanks to ARIMS, inventory levels and the flow of materials are always under control.
This seamless procurement process is based on SmartBins, materials containers with integrated weight sensors that continually measure current inventory levels. As soon as reserves dip below the re-order threshold, a pre-arranged top-up consignment is delivered to the customer.
The right amount at the right time
Up to now, Bossard has defined the re-order thresholds and top-up volumes semi-automatically with the aid of the ARIMS system – a laborious task involving thousands of items, compounded by the fact that the configuration of parameters is dependent on multiple factors, including manufacturing volumes, storage costs and outlay for delivery. Regular alterations to production processes and potential spikes in consumption represent particular challenges, as supplies should never run out. In short, it is hard for human staff to keep track of all of this.
Bossard therefore set out to automate optimisation of the procurement parameters. The result was SmartOrdering, a system that constantly analyses consumption of C-parts and uses machine learning to automatically define ideal re-order parameters.
“Thanks to SmartOrdering, express deliveries fell by 70 per cent, with no increase in inventory levels.”
The question of “what?”
The first step was to visualise the data in order to gain a complete overview of all the information, including inventory throughput and the timing of re-orders and deliveries. This helps make the data more comprehensible and will later make it easier to track and trace.
But what constitutes a “good” configuration of the parameters? What exactly should be optimised? These are the key questions. All kinds of frequently contradictory cost drivers are in play. For example, Bossard’s customers would like both lower inventory levels and fewer consignments of C-parts, although smaller storage facilities by definition necessitate more deliveries. So, where is the economic sweet spot to be found?
Ergon designed a mathematical model that combines the cost drivers. In addition to the outlay for storage and delivery, the risk of inventory shortfalls is a key factor here. Unsupervised machine learning computes this risk, thereby quantifying the costs for express deliveries. Optimisation on this front minimises overall costs and allows an ideal re-order configuration to be established.
As a further step, a Python prototype was tested out with 15 clients, incorporating approximately 10,000 items and, in certain cases, more than ten years’ data history. The results were checked in close cooperation with Bossard and compared with ARIMS. The findings were promising and SmartOrdering output was tested in a pilot phase involving 30 clients.
The bottom line is remarkable: the number of orders required by the test clients dropped by 26 per cent and express deliveries fell by 70 per cent, with no increase in inventory levels. Ongoing improvements were made to the system based on the experience gained during the pilot phase and it was rolled out in stages for additional clients.
Added value for all
SmartOrdering automates the configuration of ordering parameters and optimises these on a rolling basis, creating substantial added value for Bossard. The machine learning technology deployed improves parameters in such a way that Bossard clients’ storage facilities are neither too full nor entirely empty. Manufacturing downtime caused by missing parts is prevented, which in turn reduces costs.