This article was published in the Ergon Magazine SMART insights 2019. Order your free copy now ->
Eugen Seitz AG, an independent, family-owned company, that has been in business for more than 60 years, has achieved international success with its valve technology. One of the firm’s departments manufactures the stretch blow moulding valves used to produce PET containers. Francesco Fini, Head of Seitz’s PET Business Unit, and Joachim Schmidt, PET Team Leader and Senior Design Engineer, explain how this process works and outline the company’s ambitions for the future.
“Seitz is a global leader in the field of valve technology for the stretch blow moulding machines used to produce PET containers. We supply machine and plant manufacturers who produce drinks bottling lines all round the world. Our valves are a crucial element in the whole PET bottle-production system. In the stretch blow process, a PET preform is moulded into a finished PET bottle using our valves,” explains Fini. The procedure must be ultra-precise, reliable and stable, and it must run at high velocity to ensure production of up to 100,000 bottles an hour.
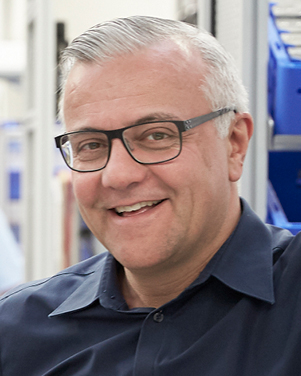
“Digitalisation is a major issue for us. We knew which direction we were hoping to go in but we wanted to use business-case workshops to get a sense for exactly where we would end up.”
Good must get better
“A customer survey carried out three years ago had suggested to us that our valves needed to become ‘smart’ (i.e. communication-enabled). The goal here was to improve our customers’ manufacturing plants, boost output capacity for machine operators and optimise our valves – that was the task we set ourselves,” Fini continues. Seitz, thus, set about developing a valve fitted with sensors in order to increase efficiency and monitor both quality and wear and tear.
“We wanted to make our products ‘intelligent’ and to network them in an “Internet of Things” solution. On the strength of a recommendation, we soon ended up knocking at Ergon’s door. We had a look around, got to know their experts, then made up our minds; we held shared business-case workshops to get started,” recalls Schmidt.
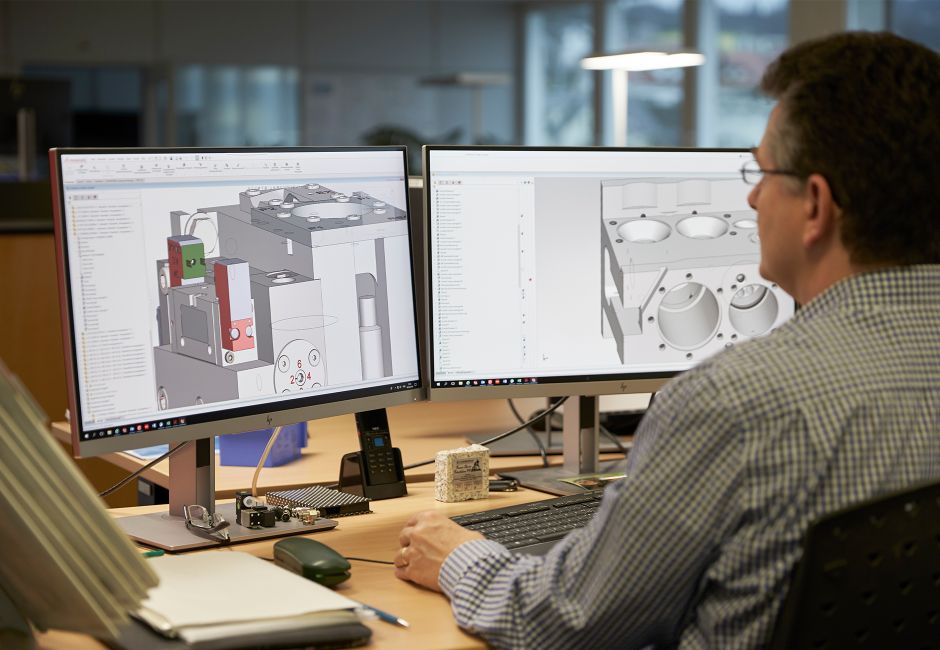
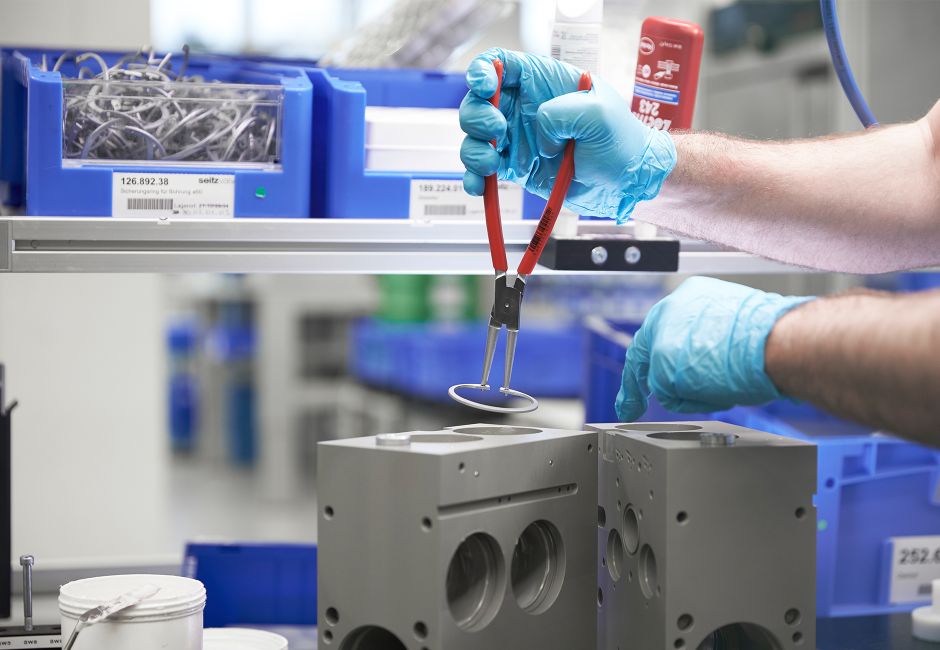
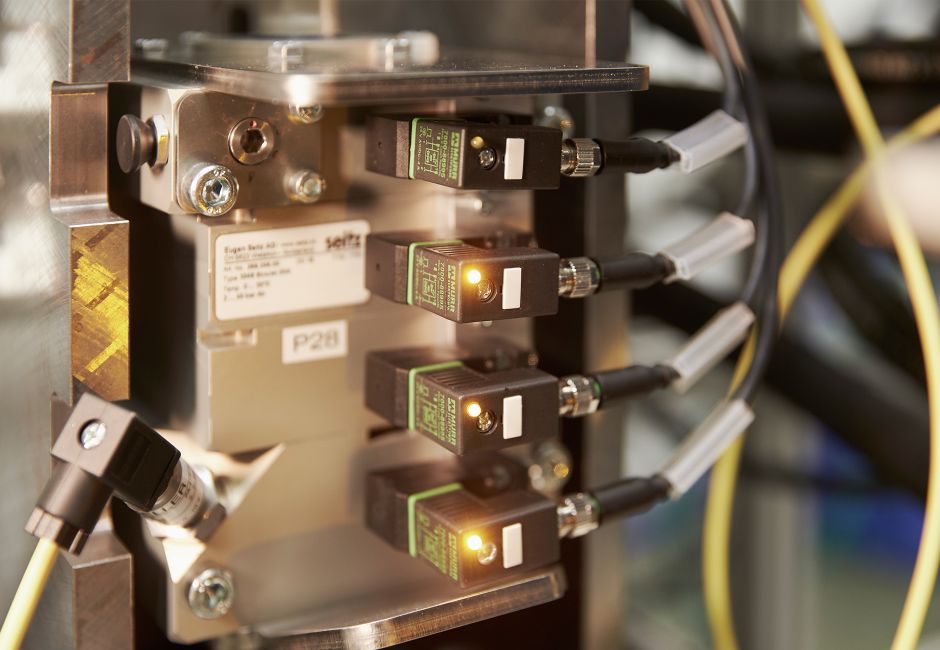
One vision and new perspectives
The core mandate was clear: the valve needed to be able to report that it was running more slowly in the event that a component had to be replaced or was faulty. The shared business-case workshops did not restrict themselves to addressing only what was possible from a technical perspective, however, entirely new business ideas suddenly began to emerge. It became increasingly apparent that the intelligent valves were collecting a lot of data, a massive amount of data, in fact, and that this information could help log the exact blowing curve – i.e. the rate at which pressure is increased – for the PET bottle, for example. High-frequency readings make it possible to collect and aggregate all production data, creating up to 2TB of data per month for each plant, which can then be analysed in even greater detail using algorithms. Where a production line is made up of many individual elements, data from additional sensors and components can potentially be deployed to optimise the entire production process.
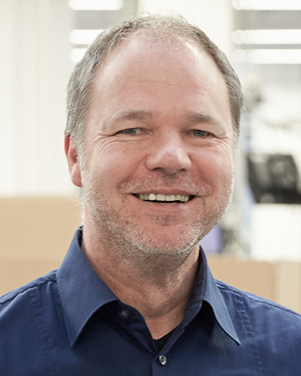
“We set about planning our ‘DAISY’ data acquisition and analysis test system in cooperation with Ergon. We developed hardware and software which we then tested in the lab – working together, with agile management.”
From valve to platform
“Our customers will always be the plant manufacturers,” says Fini. “But to be in a position to make our product better, we have to analyse the entire production process and focus on the needs of the end user. We found that out while working with Ergon,” Schmidt adds: “Our project is open-ended; we haven’t reached a conclusion. We have lots of questions to which we don’t yet know the answers. One thing is clear though: our clients are looking for added value, and we are working on generating this to the best of our ability.” As speed is of the essence in rapidly evaluating new ideas with a prototype, a private, yet open and expandable, platform was set up for Seitz based on Ergon’s tried-and-trusted core cloud solution. This made it possible to take the next step in developing a product with agile use of several generations of prototypes.
The DAISY test system
Seitz and Ergon took an agile approach to constructing the DAISY test system. It consisted of multiple rounds of workshops, results validation, lab research, software adjustments and ongoing development work. Seitz divided the project into three key phases; DAISY set-up for a feasibility study, DAISY operation to collect findings, and future application of findings for a mass-production solution. “We embarked on this project with no fixed expectation of what the end results might look like. This was quite new for us,” admits Fini. “But we knew that we wanted to carry on making the best valves and to deliver even better value with smart valves so that our customers can buy both mechanical components and software all under one roof.”
Key points at a glance
Idea & concept
- Work up business case
- Analyse potential customer benefit
- Develop high-level roadmap
- Agile approach
- Prototype for demo to external pilot clients
Approach
- Evaluation of hardware and data acquisition components
- Private “Internet of Things” cloud set-up (Ergon core cloud)
- Connection of test devices
- Custom user interfaces in Seitz corporate design for range of user groups
- Test phase, ongoing fine-tuning, optimisation
- Cloud application goes live (prototype)
- Next up: integration into production facilities (pilot phase)
Challenges
- Real-time operational data capture
- Innovation leadership and differentiation
- Enhanced commercial success
Wow
- Pressure curve for PET production is visible globally and in real time
- End-to-end: from data acquisition with an industry PC to the cloud, and on to the browser to visualise data
- Time to market: less than six months from idea to functioning prototype
- Any number of plant set-ups can be operated via the cloud
Interested in more?
Digitisation projects
Change makers
Tech trends
Order now
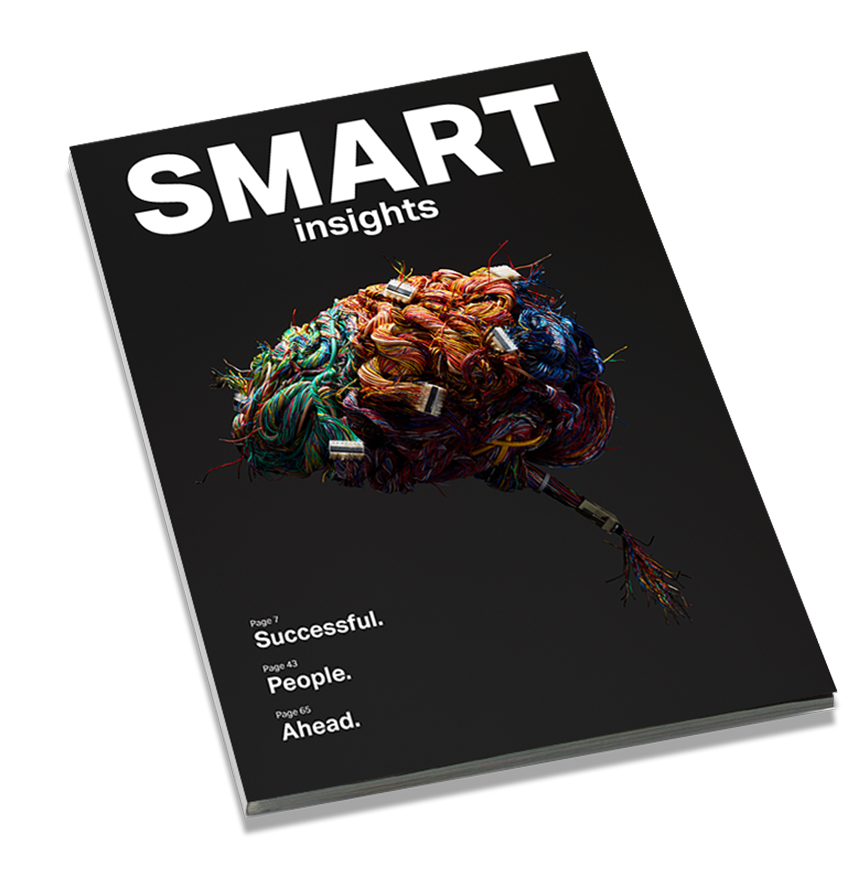