This article was published in the Ergon Magazine SMART insights 2019. Order your free copy now ->
Production lines are complex machines. Once they are started, they run perfectly but all it takes is a change from one biscuit variety to another and the whole thing can grind to a halt. A technician is called to reset everything and only then can work be resumed. Wouldn’t it be more efficient if staff on site could pull the levers themselves? The ever-popular Blévita cracker gave Ueli Eggenberger, head of IT at Meilen-based Midor, a brilliant idea …
Getting better and working more quickly, with fewer rejects and less wasted time, while always retaining the same high quality – such are the constant challenges facing Midor, who are part of the Migros Group and Swiss market leaders in baked goods and ices. “It’s always been like that,” says Ueli Eggenberger, “but it’s part of my job to identify untapped potential when it comes to optimisation and to come up with useful solutions to impress our product managers.”
A tradition of innovation
Blévita cracker production had already been selected at an early stage to trial a new innovation – at the time, the hot topic had been the Internet of Things (IoT). “For me, an IT engineer with a penchant for tech and craftsmanship, digitalisation, especially Industry 4.0, presented a particularly interesting challenge. Back then, the key consideration was not to lose precious time having to wait for the manufacturer’s technicians if the production line went down. We wanted to use technology to equip the staff on the ground with new skills. One quick call to an expert and future breakdowns can now be sorted out quickly with the aid of IoT under the instruction of a professional,” says Ueli Eggenberger.
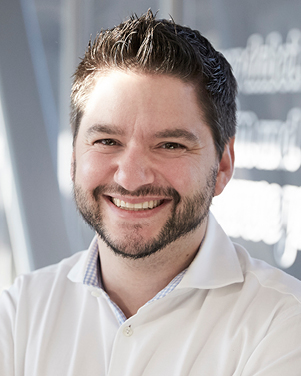
“Optimisation of human-machine interaction is a big issue for us. We wanted to find out what potential we could mine with AR.”
Going a step further
Blévita crackers are available in more than 39 varieties and all kinds of different packaging sizes. In the past, production has had to be stopped in the event of a switch from one variety to another. While technicians who can reset the machinery are typically on call somewhere on the premises, they cannot always be on the spot immediately. The upshot? A halt in production and a loss of time and efficiency. “We produce 1,700 Blévita crackers per minute, so speed and efficiency are critical when there’s a fault,” explains Eggenberger.
This raised a host of questions. How can you ensure that the staff in the immediate vicinity are able to make the necessary adjustments quickly and easily? How can you create an instruction manual for a group of people made up of 43 nationalities with a Babel of different languages? People who were often from the younger generation, who don’t read manuals and prefer to watch videos, and so are far more familiar with moving images than with static text?
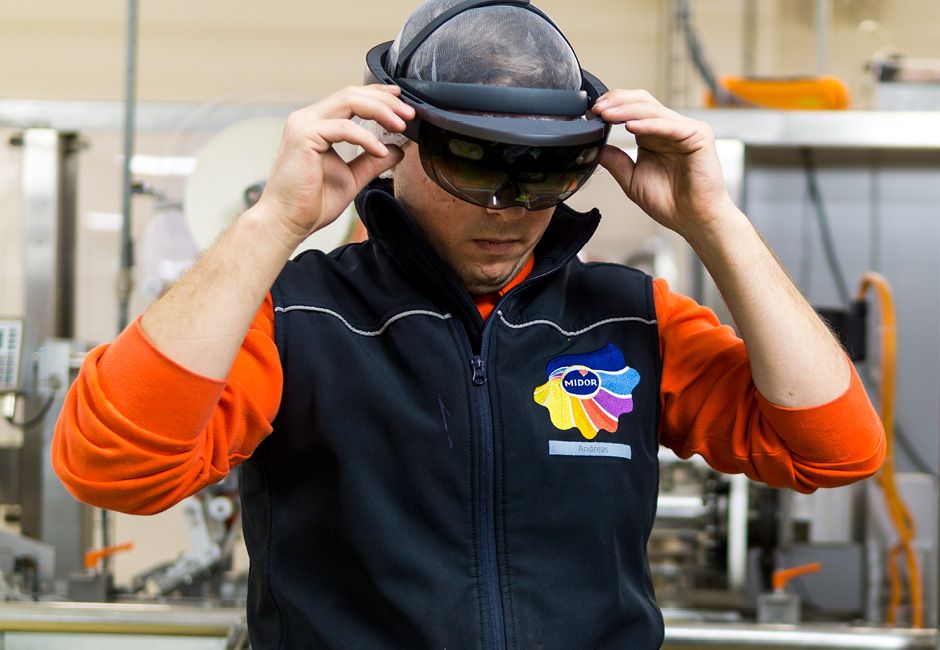
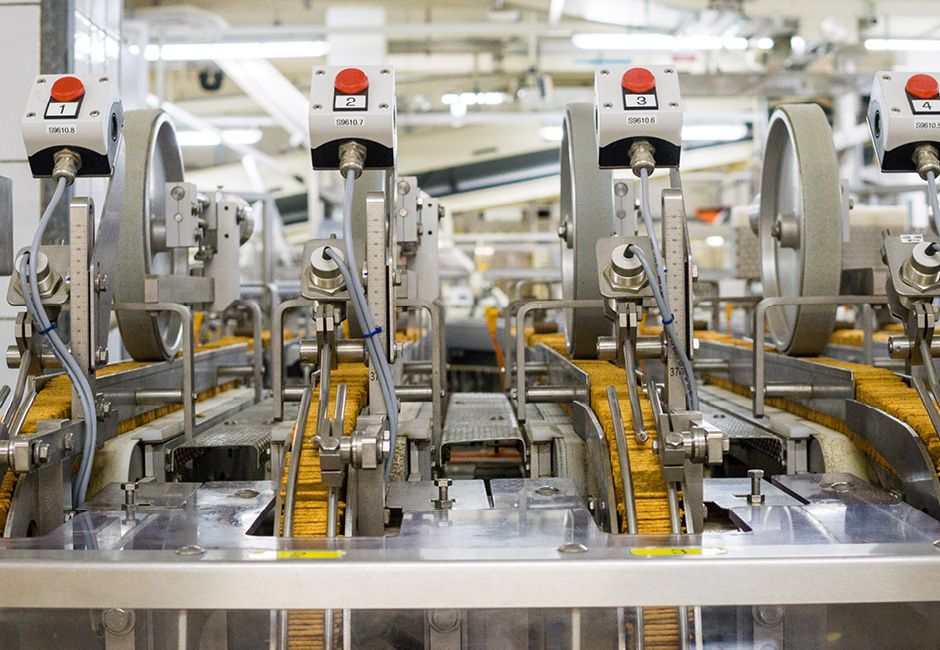
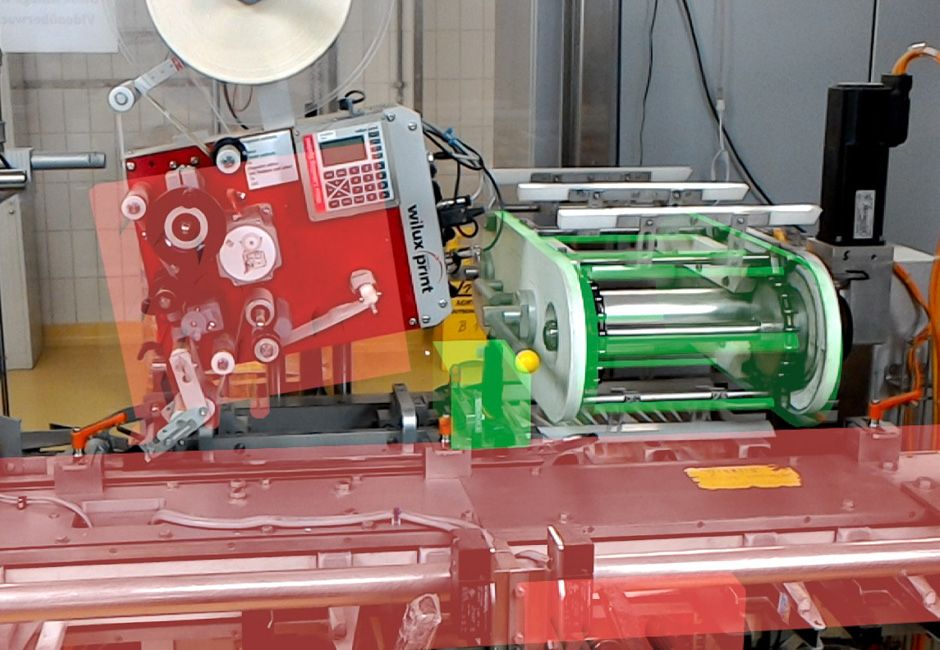
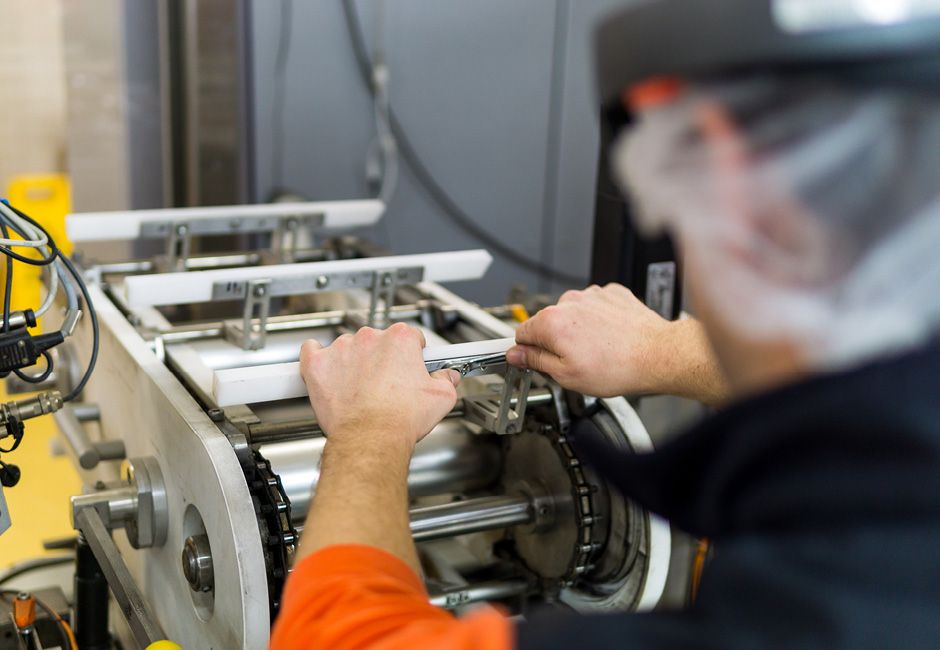
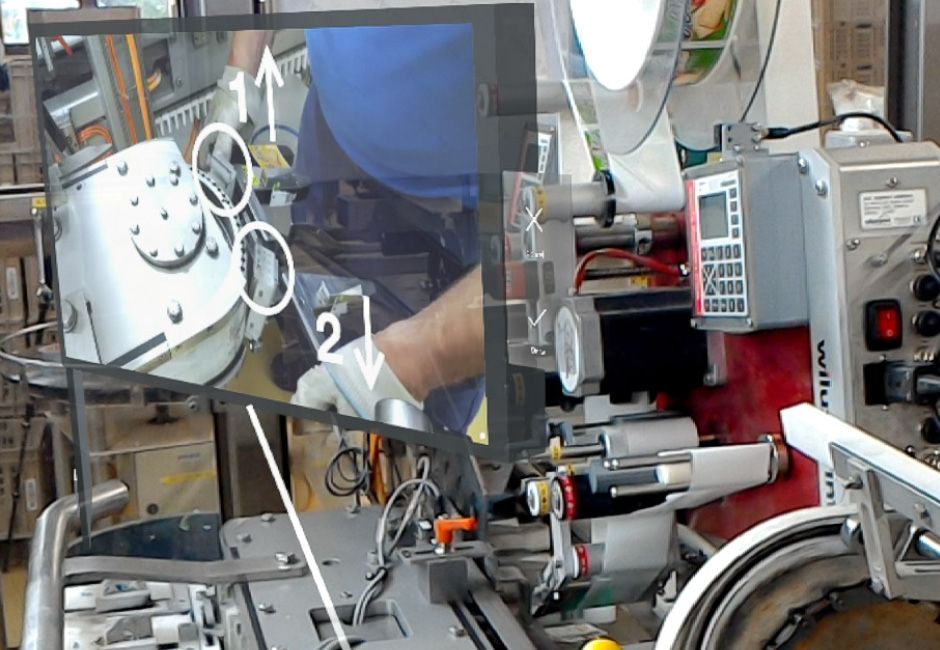
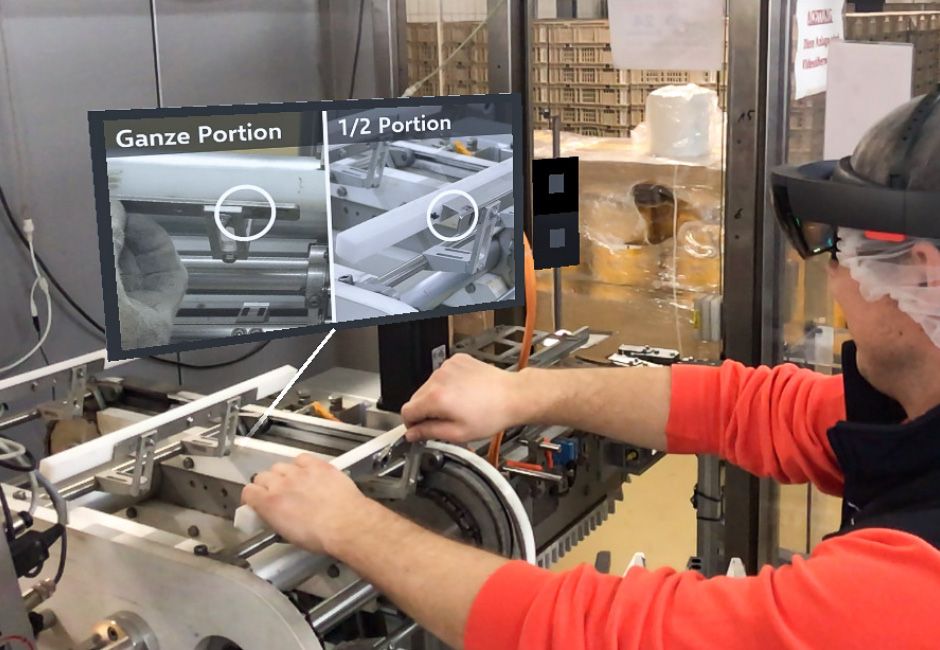
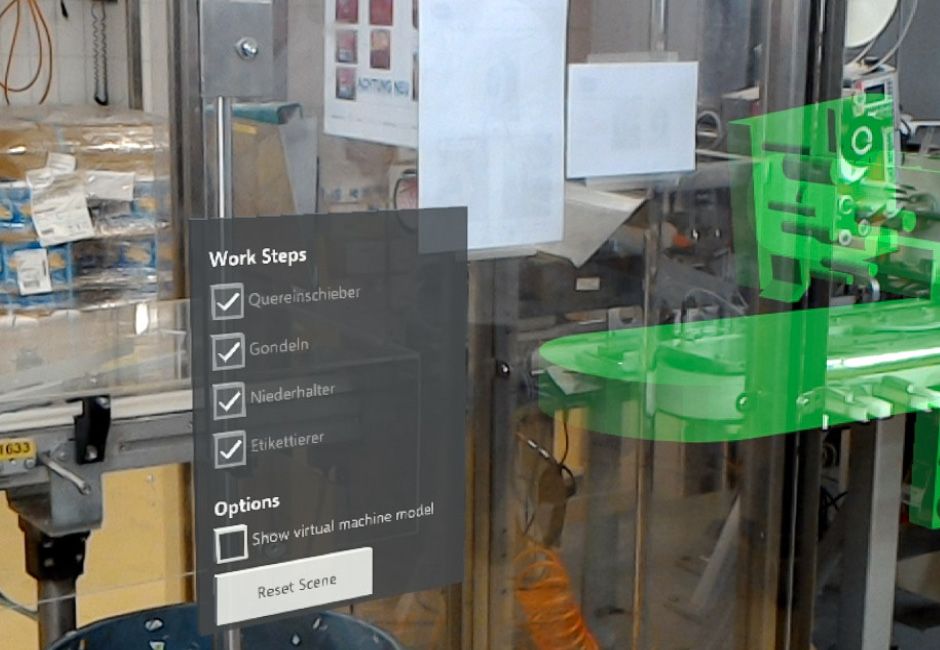
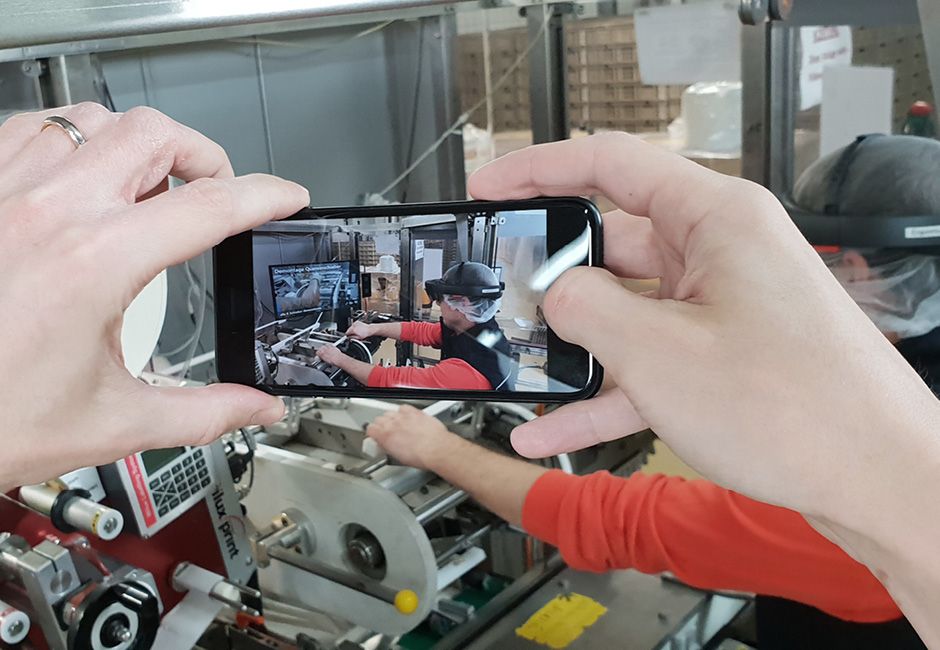
Theory is thorny, practice is persuasive
Ueli Eggenberger attended a talk by an Ergon representative on the topic of augmented reality (AR) at a symposium and his interest was piqued; an agreement was reached in the ensuing one-to-one conversation to get to the bottom of the matter and to work together to develop a satisfactory solution.
An approach soon crystallised: they needed to create a prototype featuring a HoloLens and AR that would take staff by the hand, as it were, and demonstrate what needed to be done quickly and clearly. Every member of staff, both young and old, had to be able to put on the goggles and reliably and safely carry out all the steps needed to restart the production line with its new specifications in the shortest possible time.
So, how does it work? Inputting new parameters involves swapping out certain components on the machine. When an employee puts on the HoloLens, the parts to be worked on are coloured red in the goggles – something had to be changed for all these components. The employee then taps on a given area and, immediately, an instructional video appears, using images to show what is to be done and where, in easily understandable terms. Once this has been completed in the real world, a checklist appears and the task is ticked off as completed. The area that has been successfully changed is now coloured green and the remaining red areas are worked on in turn, step by step. The video shows you how and the checklist documents your progress.
Who invented it?
This question never arose. From the outset, the unique and impressive thing about this project has been that both sides, Midor and Ergon, have shown genuine enthusiasm, working in an uncomplicated and cooperative way to find a compelling solution together. “Those aren’t just empty words,” says Ueli Eggenberger. The Ergon specialists involved are delighted with the outcome, as are Midor’s production specialists. Thanks to this prototype, they can now get hands-on experience and see precisely what advantages AR can bring – now, and especially in the future. “The prototype we have worked up is important as it enables us to demonstrate our technological innovations one-to-one and in a way that is easy to understand; both in-house and further afield. At our company, IT is extremely active whenever business processes need to be optimised sustainably,” says Eggenberger.
Key points at a glance
Challenges
- Making complex instructions understandable for everyone
- Location/language-independent
- Usable in a noisy environment
- Easily expandable
- First-class demonstration tool
- Cost-effective solution
- Can be demonstrated one-to-one for production specialists
Idea & concept
- Create prototype
- Display short video instructions on virtual screens in a HoloLens for all the relevant parts of the machinery
Approach
- Creation of video instructions: expert demonstrates work steps on a machine on-site
- This will be displayed as a hologram on the machine as a video.
Wow
- Specialist audience can simultaneously watch what is happening in the HoloLens on an iOS app
- The HoloLens recognises the position of the iOS device
- Interaction of the person with the holograms can be synchronised between the iOS device and the HoloLens via a network
- Observers can view what is on the app, one-to-one, while simultaneously watching what the person on the ground can see in his HoloLens, and can inspect how the prototype works from outside (pictures 6 + 8)
Interested in more?
Digitisation projects
Change makers
Tech trends
Order now
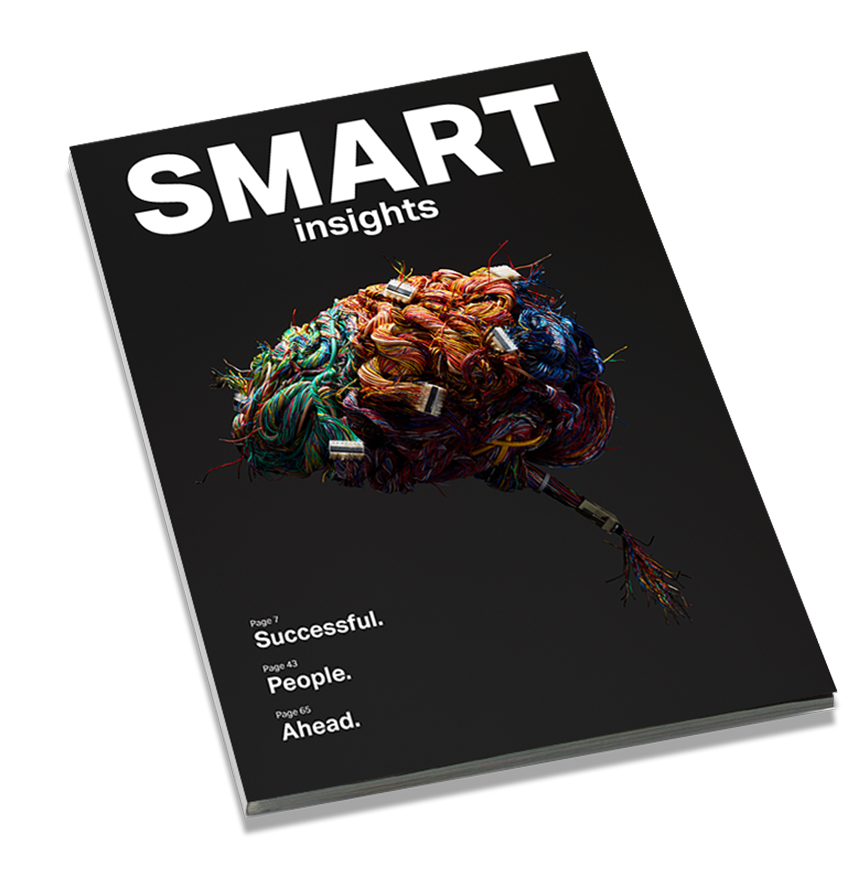