Web application for controlling material flow
Zürich, 14.08.2015 – Bossard Reference
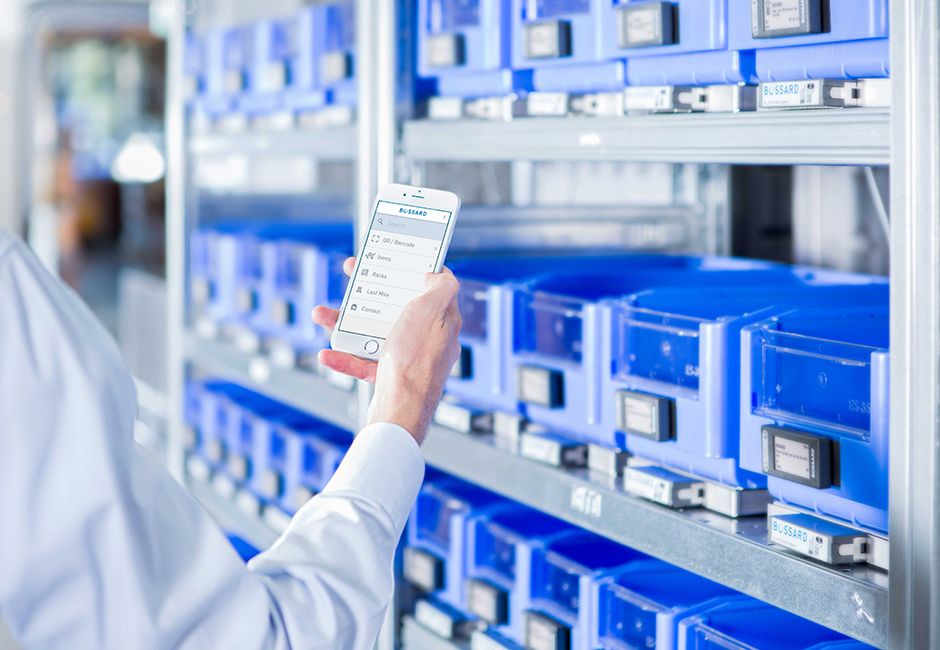
When installing devices and equipment, countless small parts such as screws, nuts or gaskets are required. These so-called C-parts cost practically nothing. But if a production line comes to a halt because C parts have run out, the resulting costs are significant. Procurement costs are very high compared to the purchase volume – which is where Bossard comes in. The Zug-based company specialises in the logistics of C parts and has developed its own software for the application. In 2013, Ergon was commissioned to revise the solution and replace it with a modern web application.
Bossard provides its customers in 26 countries around the world with logistical concept support to help them to set up and optimise new production lines, key to which are optimal design, sizing and layout of C part containers. Since the late 1990s, these containers have been monitored by SmartBin. SmartBin is a fully automatic system developed by Bossard that combines conventional storage containers with weight sensors and continuously transfers the quantities to Bossard. As soon as the weight falls below a certain level, new parts are automatically delivered to the customer.
Beginning in 2000 Bossard began developing ARIMS, an in-house software solution that helps stock production lines, processes data from scales, and triggers orders. The software is also used for customer administration. As the years went by, a complex, comprehensive and fully automated procurement system emerged.
Web application instead of Delphi software
In 2013, Bossard decided to rebuild ARIMS: "The system still worked well, but maintaining the Delphi software was expensive. That's why we wanted to switch to a modern platform, before problems arise,” says Urs Güttinger, CTO. The invitation to tender for the web application, which allows all customers and employees quick access to the material flow, was sent to several software companies. After a multi-stage evaluation, the contract for the new development went to Ergon, whose know-how, highly qualified employees, modern development methods and associated references were impressive.
Software archaeology
One of the software’s important functions is automatic order processing. Over the years, various special cases have been mapped, and a highly complex system has been developed. To make sure that the details from the previous system were not lost, Ergon analysed the Delphi code for order processing line by line and created a specification.
Offline-capable
An important requirement for Bossard was that the new software be web-based yet still offline-capable, since the logistics specialists work for customers in some places without an internet connection. The software engineers at Ergon solved this apparent contradiction with a few twists: If a customer visit is planned, the required data is copied to the local computer in advance. The employee then starts ARIMS at the customer site by double-clicking on the application icon. The browser opens, and the user feels as if he is online. The browser connects to the locally executing system – a similar system is initialised in the background, as is the case when online.
Tested in parallel operation
In spring 2015, the new application at Bossard was put into operation in parallel with the existing one. This ensured that the new system produced the same results as the old one. Following parallel operation, the old system was taken out of service. The new solution has proven itself in practice and is constantly being developed.