BIM goes Augmented Reality
02.09.2021 – Computerworld
Article for Computerworld, 27 August 2021
Building information modelling is a big asset to construction. As a digital twin, its 3D data can be visualised on site using augmented reality. The technology is versatile, portable and easy to use.
The Felix Platter University Hospital for Geriatric Medicine is the second-largest hospital in Basel and an outstanding centre of inpatient and outpatient care. In 2018 it moved to a new building that is unique not just as a hospital, but also from the construction perspective. It was one of the first projects in Switzerland that made consistent use of building information modelling (BIM). BIM is a digital model that stores full information on the building under construction. The model reflects the entire process chain from the initial project through planning, completion and documentation. It works by creating a digital twin of the physical building.
In the case of the Felix Platter Hospital, the BIM method “was a major factor in ensuring that the building was completed on budget and on schedule with a build time of just four years”. That's the verdict of consulting, planning and project management firm Drees & Sommer, as well as lead architects wörner traxler richter with Holzer Kobler Architekturen. BIM not only allows all subcontracted work to be visualised within a building, but also delivers information on project flows, costs, and build progress.
BIM is a game-changer
BIM holds enormous potential, especially in a construction sector seen as relatively un-digitalised. The approach will continue to establish itself until it becomes standard. However, to date BIM has mainly been an office-based solution with architects and construction engineers the primary beneficiaries. The professionals on site, and building subcontractors in particular, have not had the support of these 3D models. That is because they generate considerable volumes of data that it takes a certain degree of computer power to process and visualise.
There are downsides to this discontinuity between office simulation and building site reality. The different elements of work and the companies executing them are tightly scheduled so that the build can progress swiftly. Subcontractors naturally have the usual 2D plans that enable them to do their jobs. But the devil is often in the detail, and without the necessary information to hand it is easy for delays to occur or mistakes to creep in. A study by the Federal Institute of Technology in Zurich documented that simply putting right all of the construction defects in newbuilds in Switzerland accounts for eight percent of all construction works annually, amounting to costs of around 1.6 billion francs.
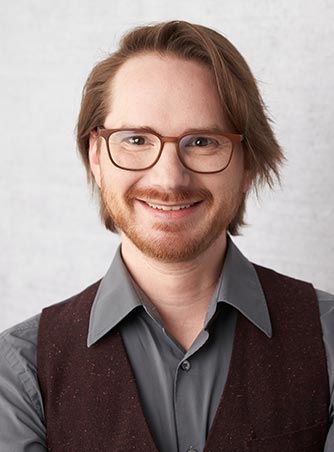
“Today, smartphones put an augmented reality device in almost everyone's pocket.”
AR right there on site
Augmented reality (AR) unlocks the full power of the data model on site, allowing the physical construction to be compared visually with its digital twin.
AR makes it possible to reconcile progress on a building site directly with the specifications of the 3D model. With BIM, the necessary 3D data is already in place. This visual information makes it easier to spot defects. You can write a wordy description of whether a door is hung to the right or left – or you can simply show that door in an AR visualisation on screen. It goes without saying that construction defects must continue to be documented in writing, for contractual reasons at least, but the additional information provided by AR makes handling those defects more efficient. Construction sector collaboration platforms have been set up to help manage quality standards and outstanding work. Technologies like these mean that pending issues can be passed on directly to the subcontractor concerned.
AR does present a new set of challenges, however. Many of today’s AR environments still look like prototypes, because they must be strictly controlled to ensure they function reliably. Applications have to be especially robust in the construction sector, where conditions are harsh and can change very quickly. For AR to be accepted as workable on site, any application also has to be available at all times, and operate along familiar, intuitive lines. AR glasses, for example, work with gesture commands that the user must first learn. In this cost-conscious sector it is also highly unlikely that we will see AR glasses widely used among subcontractors in the foreseeable future. For now, they will remain reserved for specific user groups such as building inspectors, and nobody else.
The beginnings of spatial computing
Today, smartphones put an AR-capable device in almost everyone's pocket. Even better, everyone knows how to use them. Smartphones create democratic access to BIM information. They represent a step towards spatial computing, in which digital content is presented in relation to space and to physical objects. This opens up innovative interactive operating concepts, quickly mainstreaming new solutions.
There is still one more obstacle to implementation, however. An app like this must be able to answer two questions before it is of any use: where am I, and what am I seeing? Without this information, augmented reality cannot accurately overlay physical reality. Automatic positioning is no small thing on a building site, where there may not be a reliable GPS signal, let alone wifi. Sensor networks can help, but they are time-consuming to maintain and their reliability leaves much to be desired. They are vulnerable to repositioning, damage and theft.
Processes that do not need any specific positioning infrastructure are much more promising. From the mathematical perspective, room corners are an effective starting point because they locate a point uniquely by the intersection of three levels – the walls. All the AR user has to do is identify this point in relation to their own rough position in the room, initialising the app by tapping the touchscreen displaying the 2D plan. These days, they can be localised within 10 to 15 seconds. Users load the BIM data they need for the site to their smartphones before they leave the office. Once on site, the app works offline.
Construction just one of many use cases
AR can already use 3D data to visualise the interior layouts of office and industrial buildings. In offices it can be used to plan the interior design, for example, determining where meeting rooms and even individual desks will go. Here, too, a direct comparison of digital data and physical space enables things like narrow corridors to be identified early on.
The advantages are even clearer in industrial buildings, because repositioning high-bay storage or machinery at a later date is extremely costly and time-consuming. AR visualisations make it much simpler to check at the design phase where there might be collisions, for instance. At this stage, moving a wall by a metre is not a problem.
There is no need to put BIM and AR back in the drawer when a building is completed either. They can be used in combination throughout its life cycle. Facility management is a prime example. If a supermarket chiller section needs maintenance, BIM data shows the engineers where all the connections are and how supply lines are routed. With this approach, the work can even be carried out by a company that was not involved in the original build.
The BIM-AR combination also benefits specialist areas such as heating, ventilation and air-conditioning. Here, engineers work on complex systems that are often hidden under plaster. They must continue to function for decades and so must be checked regularly. Real-world data on these systems is collected and stored continuously in major buildings. It offers greater visual support for these checks because AR makes it easier to allocate that data to the individual system components. In retail buildings, for example, AR visualisations can help to verify that fire safety and escape route regulations are met. An AR app can do a target-actual comparison and highlight critical points.
For building information modelling, augmented reality creates a new type of added value that is reflected in efficiency, flexibility, lower costs and higher quality. It means that components and building parts can be identified and referenced in the context of the physical space. 3D data is used not just for architectural modelling, but also to provide information at the very place in which it is needed. The technology holds enormous potential. Will future new build projects be able to manage without it? That’s hard to visualise.