Taking the smart route to a perfect PET container
07.02.2019 – Reference Eugen Seitz AG
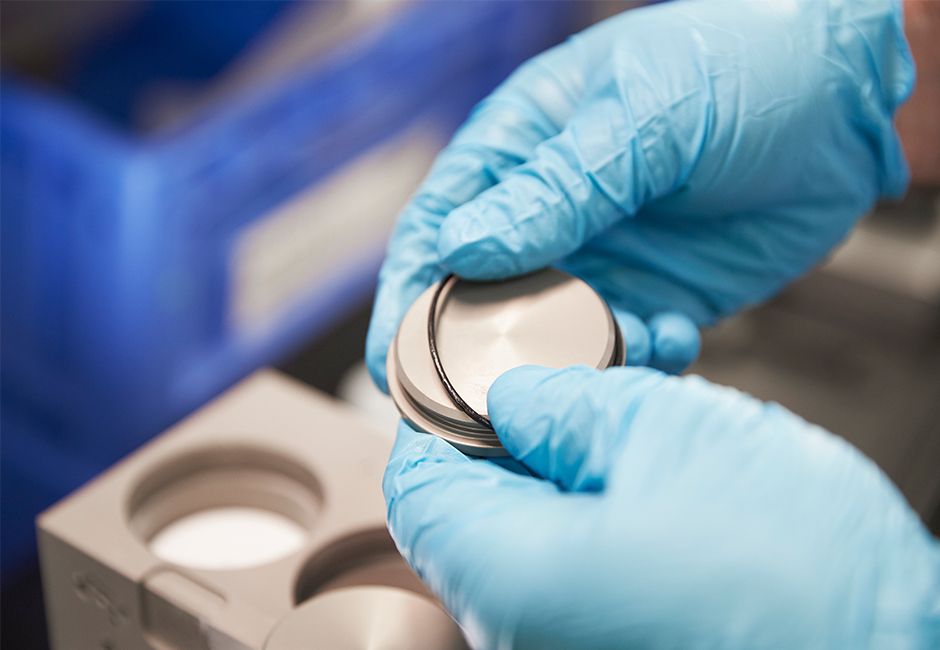
Eugen Seitz AG is a market leader in the field of valve technology for the stretch blow moulding machines used to produce PET containers. From its headquarters in Wetzikon, the company supplies machine and plant manufacturers who produce drinks bottling lines all round the world. To ensure ongoing improvements in the valves, and, thus, in the manufacture of PET containers, Seitz sets out to equip its machinery with smart technology in order to deliver greater customer value.
The stretch blow process involves using Seitz valves to mould a PET preform into a finished unit before it is filled with liquid. The procedure must run at high velocity to ensure production of up to 100,000 bottles per hour/plant and it has to be ultra-precise – safe use of the product throughout its lifecycle is predicated on perfectly distributing the materials employed across the thickness of the bottle walls. This is all the more important given that bottles these days are being made with thinner walls for environmental reasons, which also means that greater amounts of PET material can be saved.
Thanks to its close relationships with its customers, Seitz is aware of the strong demand for communication-enabled valves on the market, with plant manufacturers and operators hoping to make use of these to achieve greater transparency and earlier identification of problems during production processes. This would make it possible to improve bottle quality, boost production rates and reduce costly downtime. With this in mind, the company set about sourcing a service provider that could help them work up a business case and make their valves “smart”.
The blowing curve as a key element
The project was kicked off with a joint business case workshop, which revealed that plotting the precise blowing curve, i.e. the graph tracking the build-up of pressure within a valve, was a vital element in implementing a wide range of use cases. In order to test technical feasibility and validate the business case, Ergon and Seitz took a joint decision to adopt an agile approach and develop a prototype.
The DAISY test system
Before embarking on questions of implementation, the precise parameters of the prototype had to be defined: the outcome was the DAISY test system, an open, extendable platform that enables agile development of the smart valve via several generations of prototypes. Using the test system, valve data could now be captured and analysed for the first time, and Ergon worked with Seitz’s experts to extract the characteristics and features of the blowing curve and make them analysable.
In the second phase, DAISY was refined in cooperation with a plant manufacturer in order to record further parameters of the production process in addition to plotting the blowing curve. Test runs were then carried out with a test rig on the plant manufacturer’s premises as well as in a genuine bottling plant in Japan. DAISY captures system data and provides plant operators and manufacturers with access to these via the cloud in the form of Grafana dashboards. Seitz can also carry out analyses using Python.
Challenges included recording data at above-average frequencies (up to ten kilohertz) and minimising delays in displaying the processed data to the plant operators – most data-visualisation services in cloud environments are typically calibrated for a maximum of one kilohertz.
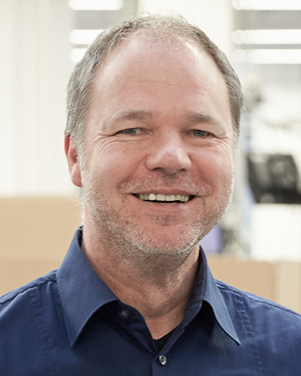
“We wanted to use smart valves to increase customer value. Ergon paved the way for this change.”
Data management in the cloud
As the data captured per plant can add up to some two terabytes (TB) per month, it was clear from the outset that a powerful cloud solution would be required. In addition to processing large volumes of data, the cloud boasts further advantages, such as agile delivery of the IoT solution and global scaleability.
To ensure that sensitive data can continue to be stored on the company’s own servers, Seitz and Ergon agreed on a hybrid cloud approach. DAISY was hosted on Amazon’s cloud solution (AWS).
Networked customer value
It took only six months for the idea to be worked up into a functioning prototype and, thanks to DAISY, pressure curves in PET container production processes can now be displayed in real time for any number of manufacturing set-ups. Connection to the network makes it possible to continuously monitor valve functionality and carry out replacement work in a timely manner should problems arise. This boosts production of PET containers, reduces consumption of materials and guarantees high quality.
In addition, Seitz now has the option to use the data acquired for rolling improvements to its valves, thereby adding even more value for customers. The next phase should see the prototype transformed into a product for which Seitz will ultimately be able to provide both hardware and software under one roof. Seitz will now be able to further consolidate its leading position on the global PET market and inspire its clientele with further innovative solutions – not least thanks to its exceptional partnership with Ergon.