Safe switchovers on the production line through innovation
01.02.2019 – Reference Midor, since 2021 Delica AG
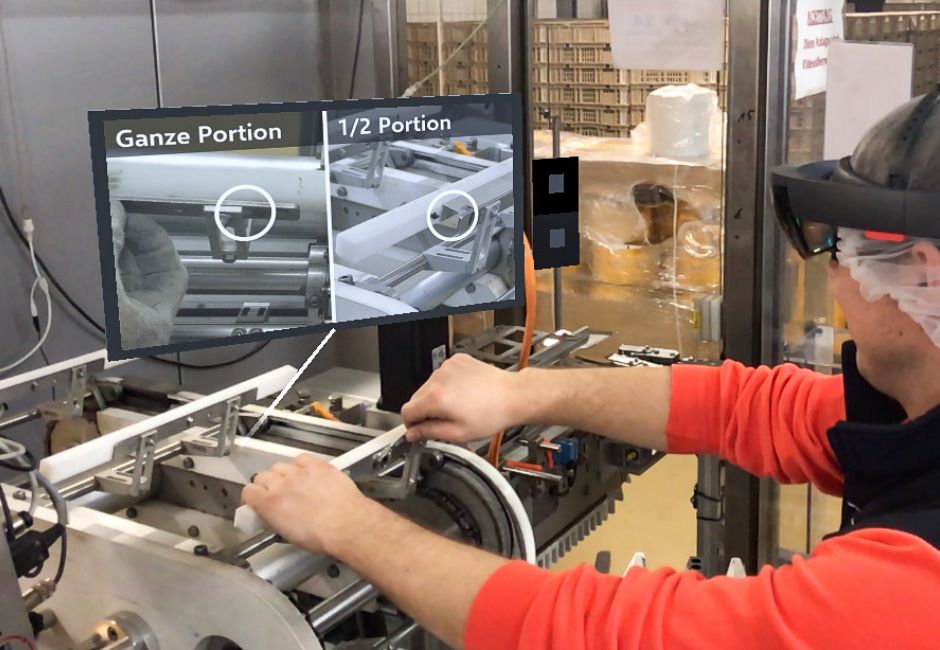
Meilen-based Midor is part of the Migros Group. Raising efficiency whilst maintaining high quality is a key issue for the Swiss market leader in baked goods and ices, so Midor is on a constant search for untapped potential when it comes to optimising its production lines. One useful solution has been found with augmented reality in the form of a HoloLens headset.
Everything has to be better and quicker, with fewer rejects and less wasted time, all whilst maintaining the same high quality – such are the challenges facing Midor every single day on its baked goods and ice cream production lines. Blévita crackers are available in 39 varieties and a range of packet sizes; when switching from one production run to another, the conveyor belts must be halted and a technician called to switch over the machinery before preparation of the new biscuit can be continued. The introduction of new technologies is intended to enable on-site staff to carry out production line resets themselves.
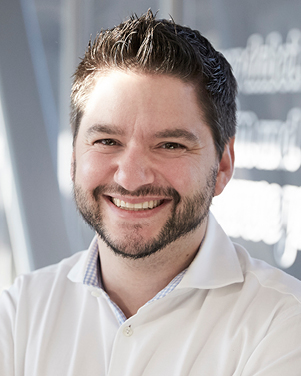
“We have worked with Ergon to develop a solution that demonstrates the considerable advantages of deploying AR – now, and especially in the future.”
Taking it a step further
Midor has worked with Ergon to develop a prototype that makes use of augmented reality and a HoloLens to display supplementary information directly on the production line equipment – thus also making it possible to interact with the machinery.
So how does it work? Inputting new parameters involves swapping out certain components on the machine. When an employee puts on the HoloLens, the parts to be worked on are shaded red in the goggles; this means that something has to be changed for each of these components. If the employee taps on a given area, an instructional video will appear in the headset’s field of view (on a virtual screen beside the person’s workstation), showing what is to be done. Once this has been carried out in the real world, a checklist appears and the task is ticked off as completed. The area that has been successfully changed is now coloured green and the remaining red areas are worked on in turn, step by step. The video shows you how and the checklist documents your progress.
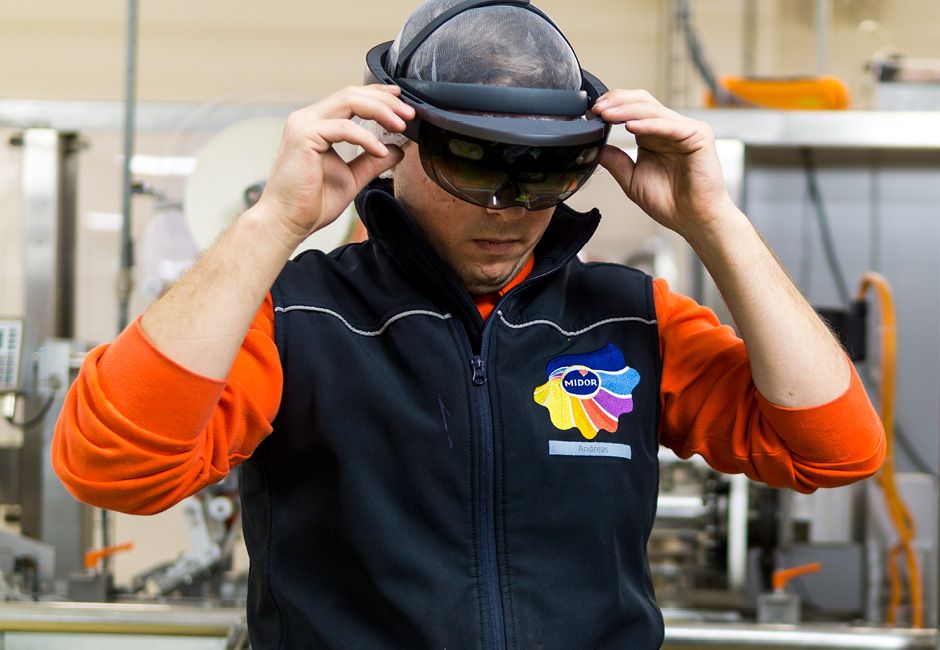
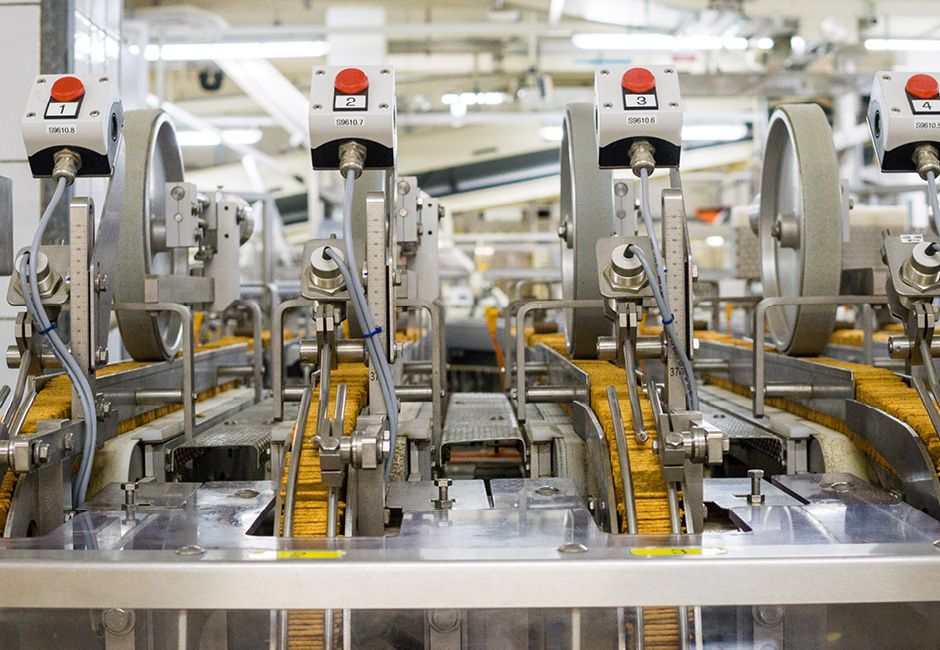
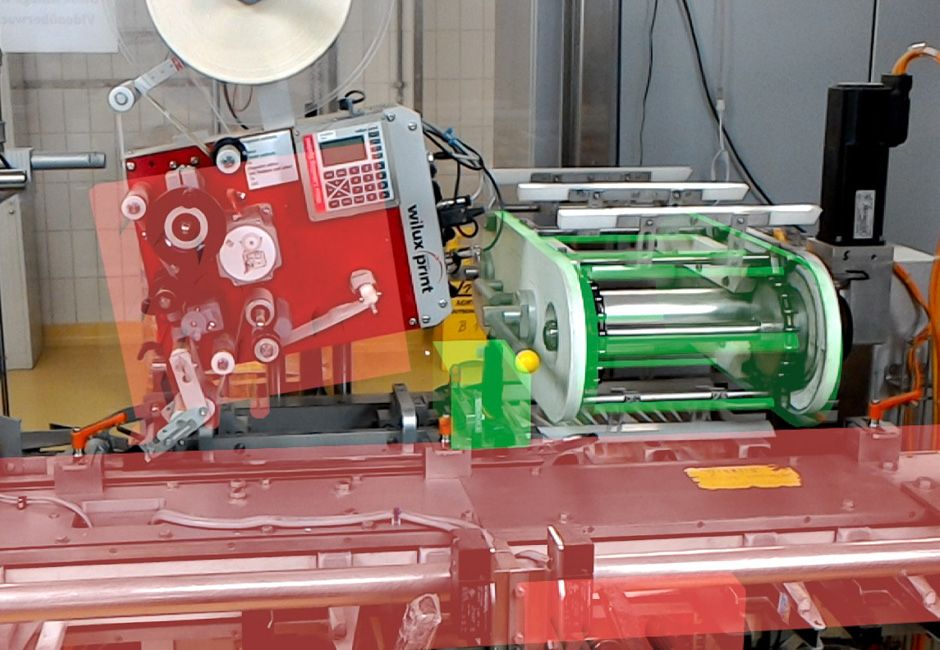
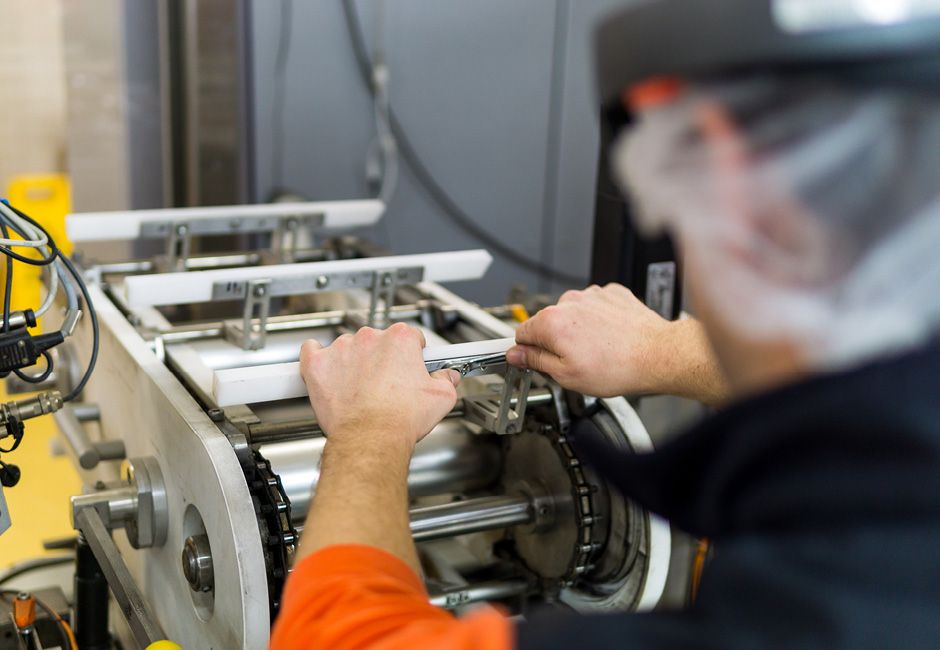
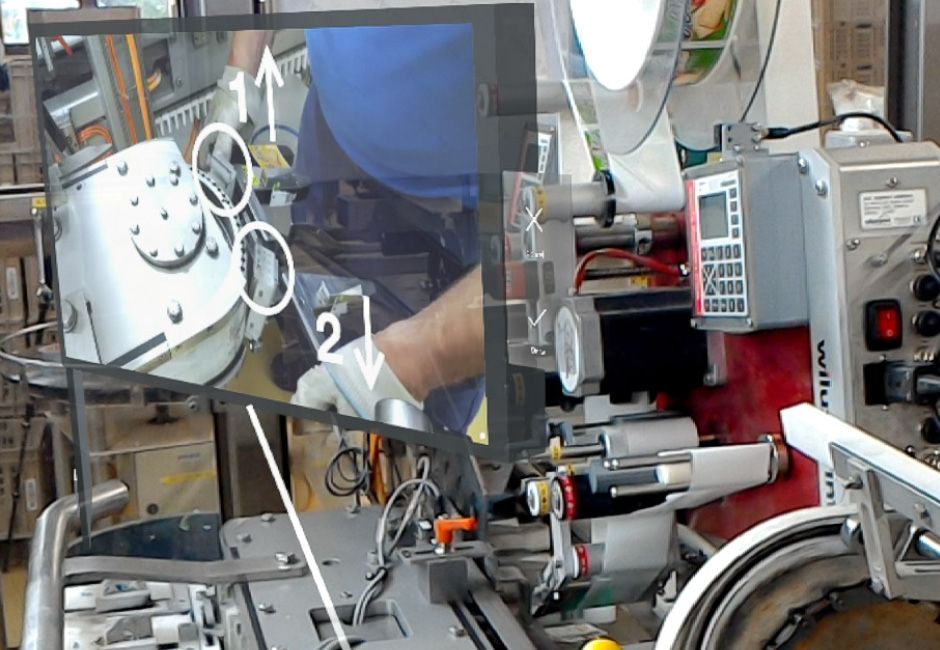
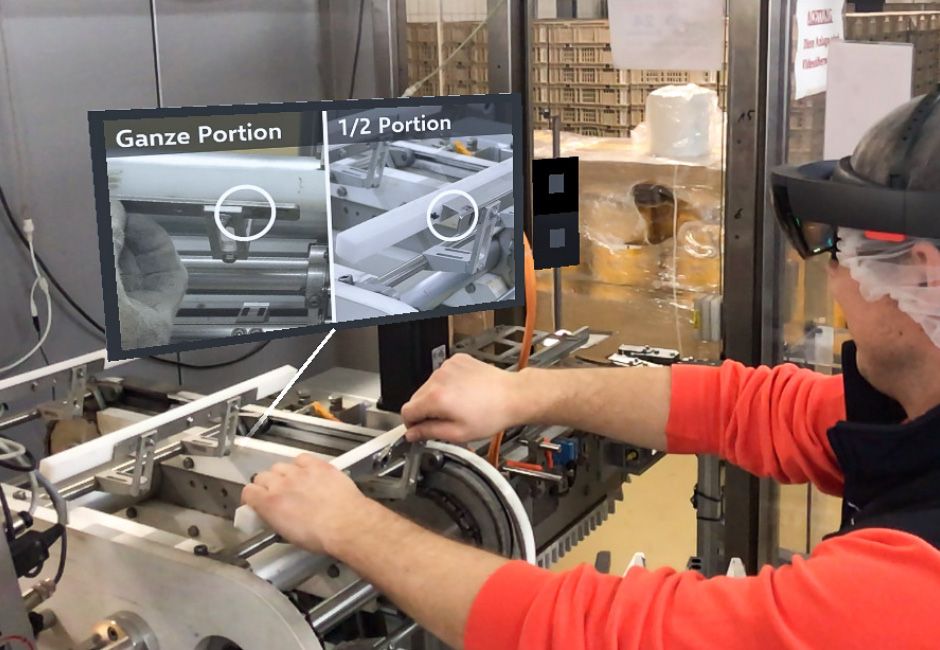
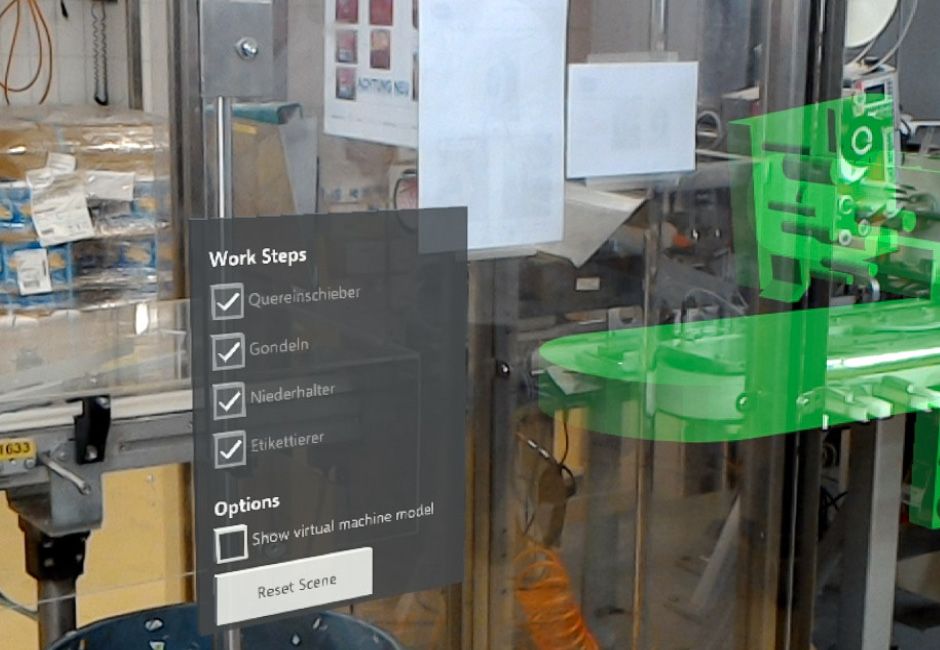
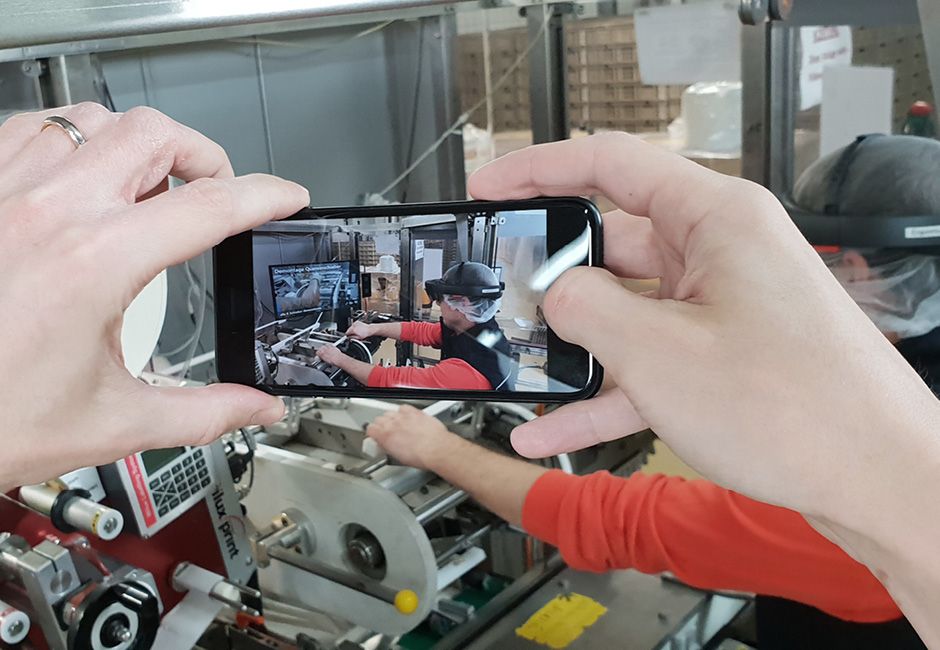
Clarity is key
Complex instructions that have to be studied hard before even starting work are a thing of the past – and the direction is from static texts towards speech-based videos. This guarantees comprehensibility for staff from more than 43 countries round the world, and the HoloLens can also be used when background noise levels are elevated.
Sustainable optimisation of business processes
When you are producing more than 1,700 Blévita crackers a minute, speed and efficiency are critical if a fault occurs in the machinery. Thanks to augmented reality and the HoloLens, any mechanically competent member of staff is able to reliably and safely carry out all the steps required to reset the machine for a different variety of Blévita cracker on their own. The production line can be restarted with its new parameters without delay, and operating downtime can be kept to a minimum. This makes it possible to deploy less highly skilled employees, not only boosting flexibility but also trimming staff costs and training budgets. Increasing efficiency and saving time sustainably improves business processes as well.