Coop: Modern merchandise management system for Coop stores
Zürich, 14.11.2013 – Reference Coop
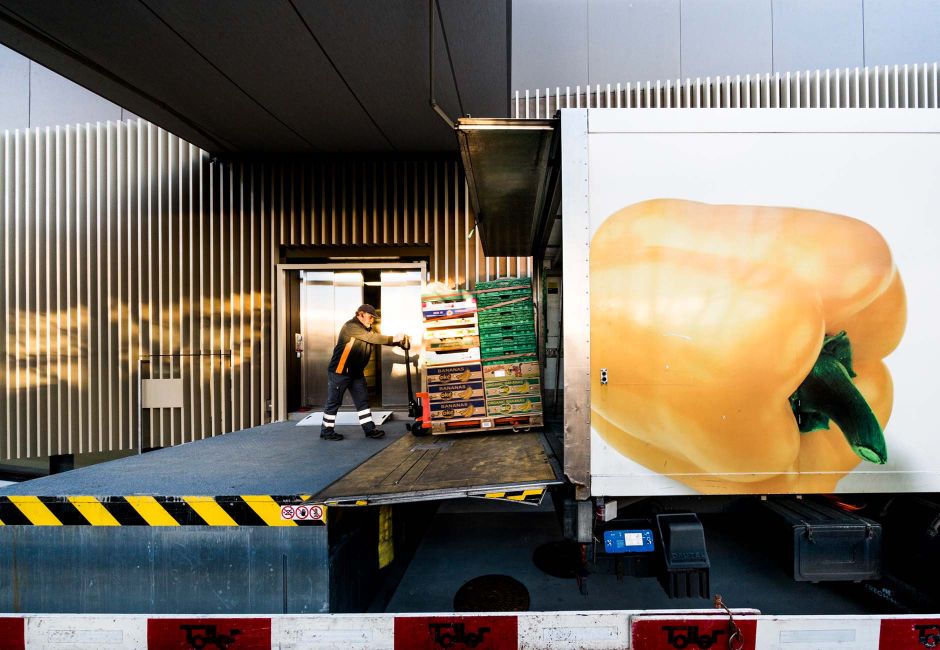
Up to 1,200,000 different articles in over 2,000 sales outlets and 530 million goods movements per week: the merchandise management processes of the Swiss retail chain Coop come up with impressive figures. The ERGO product management solution, developed by Ergon especially for Coop, makes everyday life easier for employees and ensures that inventory information in all stores is always up-to-date.
For retail trade companies such as Coop, merchandise management is a complex matter. The right amount of each product must always be available. Bearing in mind that an average Coop store offers more than 30,000 items at the same time, it is clear that an intelligent solution for merchandise management is needed. Since August 2013, the ERP solution specially developed for Coop has been in operation in all Coop stores, replacing the previous solution.
Employees at the heart
Speed and ease of use coupled with modern architecture were the key requirements for Coop. They also wanted to significantly reduce operating expenses and continue to use the roughly 6,000 mobile data entry devices (MDEs) in operation.
The ERGO front-end solution, together with the middleware CISP, integrates seamlessly into the existing SAP system and other back-end systems. This enables the near real-time recording of all relevant processes in the stores. Even more complex operations can be captured easily and quickly with mobile devices. This includes the movement of foodstuffs from the point of sale to the associated restaurant, depreciation, recalls, personal use or the combination of goods in gift baskets.
ERGO offers its own process for inventory corrections. If a non-plausible condition is found in the SAP system for a specific product, e.g. negative stock, an employee is sent on an inspection tour after the shop closes: he counts the items manually and enters them into his mobile device on site. Spontaneous counts are also possible.
"Ergon is a perfect partner to create in-house developments."
Mobile entry devices
A particular challenge for Ergon was to implement the modern solution on the already somewhat older hardware of the existing MDE. In order to avoid delays when capturing and transferring the data, a high-performance software architecture was chosen.
The data transfer happens almost in real time. As the mobile device is constantly synchronising independently, the user always has all important data available offline too. If, for example, the user is in the warehouse without a data connection, he can still use all the functions of the device.
Since an intuitive operating concept for the mobile devices is particularly important in daily use, the user interface was based on the look and feel of smartphones. In addition, the different processes are characterised by clearly distinguishable colours.
Customised mobile store solution
Thanks to its modern, high-performance architecture, ERGO more than fulfils its set requirements. The central integration and control platform enables all systems to be connected. The modular development framework also ensures that new requirements can be responded to quickly and with high quality. New data entry devices and new applications are easy to integrate. Process-controlled operations make work easier for employees and allow for quicker and intuitive workflows.